An approximate 38,000 square-foot, two story office building, constructed in 1991, exhibited significant wall and floor slab movement by 2016. A manometer survey performed in 2016 indicated about 4-½ inches of differential settlement at the south and southeast section of the building and up to 1-¼ inch cracks along the south and southeast wall and ceiling areas. The building construction consisted of exterior concrete tilt-up panels and interior steel columns, both supported on shallow foundations. Glass wall panels were also located along the exterior walls with some of the panels requiring replacement due to glass damage from the wall movement. Four soil borings, advanced around the perimeter of the building in 2016, showed about 30 feet of fill had been placed at the south and southeast area of the site prior to construction of the building. Another manometer survey performed in 2018 showed an additional ½-inch of differential settlement had occurred over the two-year period, suggesting that the building was continuing to settle. Based on the manometer surveys and the geotechnical borings, the source of the settlement was determined to be from foundation movement at the south and southeast exterior walls due to the deep fill at this area of the site. Given the amount of settlement and misalignment of the tilt-up panels, the ideal remedial method would first stabilize the structure and then potentially lift the walls back toward the original elevation. After the lift operations, void space created under the interior floor slab and wall footings would require filling. The site grade near the south and southeast exterior walls generally consisted of about 10 feet of level ground until an approximate 2:1 (horizontal to vertical) slope extended downward for about 60 to 70 feet. With the site grading conditions, construction equipment access was limited at the wall areas requiring underpinning. Given the access limitations and other project challenges, a combination of push piers and helical anchors were selected as the optimal solution for underpinning, lifting, and lateral support of the tilt-up panel footings. The south and southeast exterior walls and a center patio area would require underpinning along a length of about 350 feet. The Model 350 (3.5-inch OD by 0.165-inch wall) push pier system with side-load retrofit brackets was ultimately selected to support and lift the tilt-up panel foundations. The service compression loads were estimated at 6.3 kips per linear foot which would require 58 push piers on approximate 6-foot centers. The lateral support for the footings during the underpinning and lifting operations would be accomplished using Model HA150 (1.5-inch, solid-square shaft) helical anchors with an 8”-10” helix configuration incorporated into the Model 350 side-load brackets at every other pier location. The helical anchors were installed at an approximate 20-degree batter (from horizontal) and were terminated when a torque correlated capacity of at least 12.1 kips was achieved. The installed anchor lengths varied from 10 to 38 feet in order to achieve the required capacity. The push piers had a 31-foot minimum depth requirement (to bear below the estimated fill depth), and a minimum final drive force of 56.7 kips was specified to achieve a minimum factor of safety of 1.5. The actual installed push pier depths varied from 34 to 73 feet to meet the required capacity. The lift operations recovered about 1-¾ inch of the initial settlement. Following the push pier lift and lock-off operations, the void space created under the footings and interior floor slab was filled with 2,900 pounds of PolyLevel® PL400. PolyLevel®PL400 is a two-part liquid urethane that is mixed and injected through 3/8-inch holes drilled through the slab to expand into a rigid foam and serve as a very light, high strength void space material. PL400 has an installed density of 4 to 6 pcf with a compressive strength of 70 to 80 psi. The underpinning, anchor installation, lifting and void filling was performed during 40 working days. Products Installed: (58) Foundation Supportworks® Model 350 Push Piers, Design Working Compression Loads of 6.3 kips per linear foot, Installed Depths of 34 to 73 feet. (29) Foundation Supportworks® Model HA150 Helical Anchors with 8”-10” helix plates, installed lengths of 10 to 38 feet and ultimate axial tension loads of 12.1 kips. PolyLevel® PL400H (2900 lb.) DeBerry Engineering associates: DeBerry Engineering associatesFoundation stabilization
Challenge
Solution
Project Summary
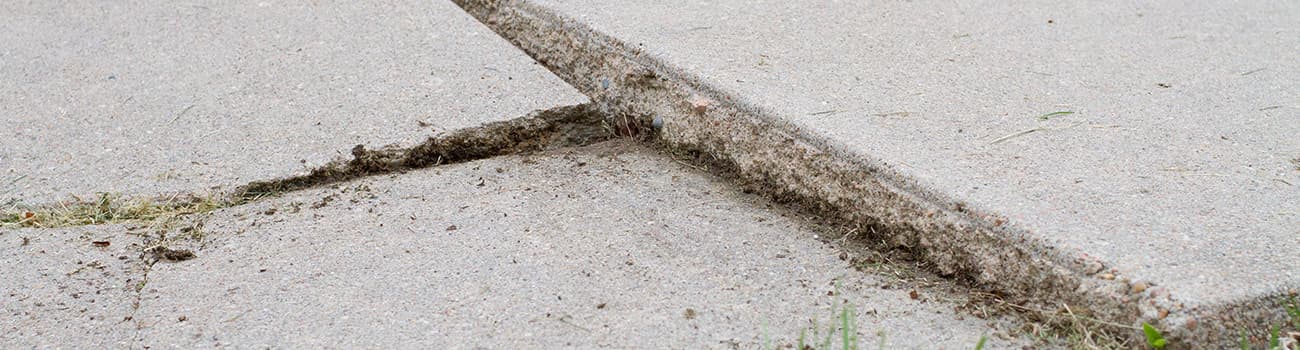
Case Studies
Friday, October 21st, 2022 by Keith Davis
View Photo Gallery
our service area
We serve the following areas
- Amboy
- Baker
- Bard
- Blythe
- Brawley
- Calexico
- Calipatria
- Cathedral City
- Cima
- Coachella
- Daggett
- Desert Center
- Desert Hot Springs
- Earp
- El Centro
- Essex
- Fort Irwin
- Heber
- Holtville
- Imperial
- Indian Wells
- Indio
- Joshua Tree
- La Quinta
- Landers
- Ludlow
- Mecca
- Morongo Valley
- Mountain Pass
- Needles
- Newberry Springs
- Niland
- Nipton
- North Palm Springs
- Palm Desert
- Palo Verde
- Parker Dam
- Pioneertown
- Rancho Mirage
- Salton City
- Seeley
- Thermal
- Thousand Palms
- Trona
- Twentynine Palms
- Vidal
- Westmorland
- Winterhaven
- Yermo
- Yucca Valley